I wanted a page where we could have a discussion and exchange information about fibers and yarns; this is the page!
I love the fibers I use, and, therefore, I love to talk about them. Moreover, I've been asked so many questions about natural fibers and have come up against many misconceptions, that I feel I must talk about them. By understanding the characteristics of the materials that we use, we can better employ them to create the exact effect we want.
For so many years, I was a knitter constantly looking for interesting yarns with natural fibers, and not finding much. When I started spinning, the world of possibilities that opened up to me was unimaginable! Until now, the enormous amount of choices was simply unavailable. So, the focus of this page will be to introduce you to, bit by bit, the options you have and to spark your own creativity.
I also want this page to be a discussion. Your input is important, be it a question, a comment, or an experience. Just e-mail me, and I will put it into the on–going discussion.
                         
Articles: (click on the title to read the article)
About Handspun
Handspun - The Number of Plies in the Yarn You Want
Wool is Not Just Wool!
About Natural Dyes
The Natural Dye Process
                        
About Handspun
I drew the analogy: You can serve store–brand bread, bakery bread, or homemade bread fresh out of the oven. Likewise, you can knit with commercially spun yarns, more specialized mill spun yarn, or handspun yarn. All of these have their right place, but given my choice, I know which delights the palate!
If you have never knit with handspun yarn, you need to try some and expect a real treat. Please look for the samples available on the yarn page.
What is the difference between handspun and commercially spun yarn?
Handspun yarn flows through your hands and feels alive. The warmth and ability to breathe inherent in natural fibers that are not machine spun, becomes apparent with the first stitch, and you know the finished garment will be cherished for generations. Handspun is like fine, aged wine from the winemaker's reserve, an original oil painting, a bouquet of fresh flowers. It's just sumptuous! Once you use handspun, you will want only to use materials produced with the same care and creative energy that you use in your knitting.
What can you do with handspun yarn?
Anything! You can hand knit with it, you can machine knit with it, you can crochet, weave, needlepoint, embroider—whatever you can dream, you can do with handspun yarn.
Handspun yarn can be customized to choice of fiber, color, thickness (size) and blend. Given the amount of hours and skill that goes into knitting and the amount of delight expected for the wearing, I look for the ideal yarn to make the garment truly special. With all the options that are open to the handspinner and the feel of the resulting yarn, the final garment can be made exactly to your specifications and be a truly wonderful work of art! You owe yourself this treat!!
If you would like to consult with me about the best yarns for your special project, drop me an e-mail or give me a call. I am happy to do custom spinning.
If you have a special pet, and would like to incorporate its fur into your garment, I would certainly be able to create a blend for you. Please look at the hat and mittens on the page of Knitting Kits—one of these was made with Golden Retriever and another from Samoyed. Coming soon I will have a separate page about dog fur!
Back to Articles List
                         
About Natural Dyes
My initial attraction to natural dyes lies in the fact that they are environmentally friendly. I use only alum, tarter, and iron as mordants. The dyes, themselves, are all naturally produced, so I don't impact the environment at all. The bonus to natural dying is that when the fibers are treated by hand with gentle materials, they aren't subjected to the harsh damaging treatment of commercial chemical dying, and, therefore, last longer!
The range of colors one can get from natural dyes is limitless and a constant source for exciting experimentation. The dyes, as well as the processes, have been used for centuries and are found in cultures world—wide. This adds to the allure of this ancient art—form and fittingly blends with the overall spirit of handspun yarn.
In fact, most of the yarns featured in the backgrounds of this web site were handspun and naturally dyed using the lighter hues.
One thing you must be aware of— natural dyes are not consistent because plants are not consistent—not from season to season, or even week to week. When using natural dyes, color can be effected by the time of harvest and even the amount of rain. Natural dyes also are affected by water conditions and temperature fluctuations. While dyes can be redone exactly as they were the first time, the color will never turn out exactly the same, so please buy enough of your yarn to complete your project.
The dyes I use include indigo for blues; cochineal and madder for reds and oranges; logwood for purples; and osage orange, fustic, golden margarite, goldenrod, marigolds, pomegranet and Queen Anne's lace for yellows. Combinations of these dyes increase the pallate and are a constant source for exciting experimentaton into new shades.
If you have a specific color in mind, let me know! I am happy to experiment for an approximation of it. I am happy to do custom orders.
Back to Articles List
                         
The Natural Dye Process
At a festival this spring, a thought occurred to me as I watched people's reactions to my products: "I'm not selling yarn, or roving, or knitting kits! I'm selling color!" It seemed, people look at the yarn, the pattern, or the fiber only after they would ooh and ah over the color. What I produce with natural dyes can be just as vibrant or just as subtle as synthetic dyes, but there seems to be a difference in the richness and depth of interest in the final product. I have had many questions concerning the process, so I decided to include it here, in The Forum.
I begin all dying with clean fresh fiber. This means that if I get a dirty, greasy fleece, right off the sheep (which is how I get fleece most of the time), I wash and dry it first, and then I weigh it. With all dyes except indigo, the weight is important in relation to the amount of mordant and the amount of dye.
Mordanting:
The first step of the actual dyeing process is mordanting. A mordant is a chemical that, when "cooked" with the fiber, attaches itself to the fiber molecules. The dye molecule, then, attaches itself to the mordant. Different mordants give different colors when combined with the same dye. For example: the dye, cochineal when used with alum sulfate gives a fuchsia color; when used with tin, the color is more scarlet, and when used with copper, it is more purple. The problem I have with all mordants except for alum and iron, is that they are toxic. Not only does the dyer have to be very careful when using them, but the disposal of the bath becomes an environmental problem. As a result, I use only alum compounds and iron for mordants. I have so many colors to explore with these mordants and different dye combinations that I find no need to add heavy metals to the water table unnecessarily!
With protein fibers (wool, mohair, alpaca, angora–animal fibers) I use alum sulfate as a mordant. This is the same alum that you get in the grocery store for pickles! To mordant, use 10% of the weight of your fiber (either, fleece, yarn, or the whole garment!). Dissolve the alum with boiling water and add this to the dye pot. Use enough water in the pot to amply cover the fiber. Bring the temperature up to 180-190 degrees F. for most protein fibers over ½ hour. Hold at temp for another ½ hour. Let the pot cool for several hours or overnight. The fiber will continue to absorb the mordant as it cools. Squeeze out the excess water, but do not rinse the fiber.
Dyeing:
Dyeing is the next step. Follow the same process as for mordanting. The temperature will be a bit less for a few dyes like madder, fustic, and black walnut. By mixing dyes, other shades and colors become possible, and applying color theory once you know what each dye does in various concentrations, increases your possibilities.
The Dyes:
Most dyes are plant materials and come from roots, leaves, flowers, tree barks, and berries. Many have long histories and were important trade items between Europe and other parts of the world. The logwood tree, for example comes from Central and South America and became an important import to both Spain and England after the Spanish Conquest. Fustic also comes from a Central and South American tree and was widely used in colonial times because of its availability and inexpensiveness. Cochineal comes from a bug which lives on cactus plants in Mexico and South America. It was always considered an important commodity and was exported to Europe from Mexico as early as 1520. Then, it ranked second to precious metals as an import. Probably the most well known dye is indigo. It has been used by many cultures all over the world and is the dye Levi Strauss & Co. based its entire business on. There are many varieties of plants that have the indigo dye in their leaves, and they are cultivated world-wide. The Picts used one variety, woad, to paint their faces blue before they went to war. The Saxons used this in combination with the yellow dye from weld to create Saxon-green.
There are some plants which grow wild in our fields and along our roadsides in abundance which are wonderful dye sources. Queen Anne's Lace and Goldenrod are two of my favorites. They give different shades of yellow and can be combined with indigo to give greens or cochineal to give oranges or logwood to give olives. To use them, pick (make sure you have permission) just the flower heads. The flowers have the largest concentration of dye. I use a 1 to 1 ratio for a medium color and 2 to 1 ratio for a dark, richer color (i.e., a pound of flowers to a pound of fiber for medium). You will need to make an extract from the flowers. Blend or chop them finely and add to the dye pot with enough water to cover. Cook them at 190-200 degrees F. for around 1 hour. Strain, reserving the liquid. Put the flowers back into the dye pot; fill with water, and do it again. Strain again, adding the liquid to the first bath. You can do this as many times as you want to extract all the dye in the flowers. Your reserved liquid becomes the dye liquer. Put in your mordanted fiber and dye in the same manner.
Here is a list of the most available dyes suitable for protein fibers and the color they yield with alum as a mordant:
- Indigo–blue
- Black Walnut–brown
- Fustic–yellow
- Osage–yellow
- Madder–red/orange
- Cochineal–red/purple
- Logwood–purple
- Cutch–yellow based browns
If you want to try dyes in powdered form, already extracted, contact The Fold, or Color Trends 5129 Ballard Ave. NW Seattle, WA 98107 phone: (206) 789-9676.
There are several good books about natural dyeing. I would recommend:
Buchanan, Rita. A Dyer's Garden, Interweave Press, Loveland, CO, 1995.
Casselman, Karen. Craft if the Dyer, Dover Publications, Inc., New York, 1993.
Wipplinger, Michele. Natural Dyes for Artisans of the Americas, Organization of the American States, Washington, D.C.,1996.
Natural dyeing is an ancient art form which gives instant excitement and gratification in wonderful color. It provides a lifetime's worth of challenge and learning to foster whatever creativity you care to colorfully pursue. Michelle Wipplinger once made a very poignant statement during a workshop; "Control your color, and you control your art." This statement has come to mind very often as I work. Hopefully it will inspire and guide your thinking as it has mine.
Back to Articles List
                         
Handspun – The Number of Plies in the Yarn You Want
The first thing I have to talk about is the number of plies needed in handspun yarn. If you have spent a lifetime with commercial yarn (or if you are just beginning and have just encountered commercial yarn) what you know is that most yarns come in 4 ply – 4 very thin strands plied together. These can be in any grist (thickness or diameter of the yarn), and the packaging usually says what needle size is most appropriate. Handspun yarn is different!
Because the fibers in handspun yarn have been treated gently in the washing, dying, carding, and spinning, and have not been subjected to harsh chemicals and high–speed machines, they remain alive! They retain their natural character, be that smoothness, crimp, shine, or fuzzy quality. These are the things that make handspun desirable, but we need to know how to compensate for them in our work because they are so different from what we have been used to.
These things have their affect on how we work with them in constructing a garment. All the natural characteristics preserved in the fiber come together to bring what we call loft to the yarn. This is a springy, spongy feeling. When wool, for example, is spun, air pockets are formed between the fibers as they twist around each other. The more air pockets, the more insulation, and the warmer the garment will be. If, through a great deal of processing, the natural characteristics of wool are removed, the fibers will just lie next to each other and twist without their natural spring. There will not be the natural loft, hence, you need more plies for warmth, and thickness,and elasticity. This is why commercial yarn is usually 4 ply.
The result of all this is that handspun yarn seems fuller. It certainly makes a warmer fabric. I'll give an example. My first handspun project was a hat and a pair of mittens made with 2 ply Jacob wool, and with them I had a brand new experience. I never got cold! I wore them in –20 º F (Yes, it gets that cold occasionally in Chicago), and I wore them in 30º F with equal comfort. It was then that I began to deduce how this could be! In the past, for the really cold weather, I used to go out in layers! (and layers, and layers)! The reason for layering was to create insulating air pockets, which I had already built in to my hat and mittens! If you add another ply or two, you are simply compounding the insulation, and it really isn't necessary, at least in most of the temperate world climates. For Barrows, Alaska, I might add another ply! Anyway, the usual number of plies for handspun yarn is 2, occasionally 3 if you want something dense and heavy.
The amount of loft in handspun yarn does have an effect on the knitting gauge. We all know we should make that 4 inch square swatch with each new yarn to make sure our gauge is right—we seldom do it, but at least we know we should! With handspun, we need to make that swatch (sorry), because each fiber is different, and the yarns react differently. Oh, don't forget to wash that swatch to really see what the yarn is going to do in the final garment.
While the number of rows remains similar to that of commercial yarn, the number of stitches per inch is different. As a rule of thumb, when comparing the same grist of handspun to commercial yarn, you need more stitches to the inch in the latter. When using handspun with an existing commercial patter (or using commercial yarn on a pattern written for handspun), you need to play with gauge and adjust needle size to the stitches–per–inch called for.
To get back to the subject of plies—with handspun, it's not necessary to use more than 2 plies, unless you want a really heavy garment, then you can use a 3 ply. If you want to do something lightweight, we can do that too! This is accomplished by using a 2 ply with a slightly larger needle, so the stitches aren't packed so close together, or you could go to a slightly thinner yarn. Much is controlled with the needle size, alone.
You notice I haven't mentioned using a one ply, or a single strand. Weavers sometimes use singles, but in knitting and crocheting, you need a balanced yarn or your garment will skew. When the singles are spun, twist is put in to hold the fibers together and make them stronger as a unit. Two or more singles are then plied together in the opposite direction from the way they were spun, and the excess twist is taken out, making a balanced yarn. A single has all the twist going in one direction, and the act of knitting or crocheting makes it twist even more; this is why weavers can get away with using a single, as the process of weaving doesn't further twist the yarn. There are some fibers, like mohair, where the excess twist can be blocked and set so it won't have that much of an effect, but I would recommend its use as an accent yarn.
Obviously, topics flow, one into the next, and I want to address them all! I think the best thing to do is have a fiber by fiber discussion so we can share information on the different possibilities available. Please write in with your questions, comments, observances, annecdotes, etc., etc., etc....... The obvious start will be wool—watch for it in April or May!
Back to Articles List
                         
Wool is Not Just Wool!
One of the great things about spinning is that you can pick and choose your fiber to exactly match the needs of your project. Over the past month, I have had an interesting experience which I want to relate. It points out, precisely, the importance of fiber selection!
Think about dogs. It seems each breed has a distinctive coat: some are long and silky; some are short and fuzzy-wuzzy; some have an undercoat of down with long protective guard hairs on the outside. All have evolved to serve and protect the animal in the environment in which they live. Sheep have the same diversity. There are fine wools, like Merino, with a lot of crimp which give softness and elasticity to yarn. There are longer stapled wools, like Corriedale, which are fine and crimpy; some, like Romney, are not so fine or have so much crimp. Wool like Border Leicester or Coopworth has a longer staple yet, but has no crimp. Instead, these have a sheen and luster that is lovely. Knowing how each wool behaves once it becomes yarn will help you select the one which is right for the garment you will be making.
For The Fine Line Sweater I selected a Coopworth fleece which I dyed in Indigo. This was my choice because the pattern was a series of cables. When doing something where the pattern will be the focal point of the garment, texture or a fuzzy quality in the yarn will only cause conflict. You need a wool with which the fibers can lie evenly next to each other in parallel fashion while being spun. The long stapled fibers are perfect for this. This is called worsted spinning. When I finished The Fine Line Sweater, I was pleased. It had the look I wanted. The shine of the wool came through; the fibers lay together so the pattern popped out; it would be warm while not too hot. Good!
Then my daughter came along and saw the sweater. "Oh, Mom," she said. "Do you suppose you could do one for me in green?" (As if I didn't have enough projects!) "Mom, it's been y-e-a-r-s since you've made me a sweater." (She spins; she knits; she even knows how to dye! I had taught the child how to fish! It was true, though, it has been years since she's gotten a sweater, and she did grow up being clothed in hand-knits!) OK.
I took another Coopworth fleece and dyed it green. I began to card it so I could spin. I was going out of town for a few days and thought this would be perfect to take with me. Hours before we were to leave, however, I didn't have enough carded, and I had to make an executive decision. I did have some green roving--all carded and lovely, ready to go. This was done out of a beautiful Corriedale fleece named Jacqueline. I went with it. It spun up wonderfully. The yarn was the same grist (thickness), so I made no pattern or needle size adjustments, and I started to knit. By the time I was about 6 inches up the back, I looked at and felt the hand of my work. There were MAJOR differences! The fabric coming off my needles was much heavier and fuller than that of The Fine Line Sweater. This was going to be more like a blanket and would be way too warm to wear as a pullover, indoors! It was assessment time.
Corriedale is a soft, fine, crimpy wool. This means that there were more fibers used to make the same thickness as the Coopworth yarn. Also, the crimp, while adding elasticity, added loft, making the yarn seem fuller. In addition, I used roving in the spinning which meant my fibers were not lying neatly parallel. I had semi-worsted or woolen spinning. Envision fibers being twisted around a column of air. This creates air pockets which make for a wonderful feel to the garment and a great deal of warmth! Unfortunately, here I had too much of a good thing!
Here are examples of the two yarns:
COOPWORTH
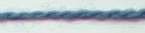
CORRIEDALE
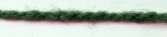
The next step was a consultation with my daughter. "Rebecca, feel this," I said. Before I could make any suggestions, she responded with delight in her eyes, "How about a jacket for winter?" So, you will be seeing Rebecca's Cardigan Jacket on the sweater page before long.
The point of this article is that when planning a garment, you have to begin with the choice of fiber. Each element plays such a critical role in the ultimate success of your project. I will be happy to consult with you if you have questions about this. It's amazing how our limitless choices can both please and confound us!
Back to Articles List |